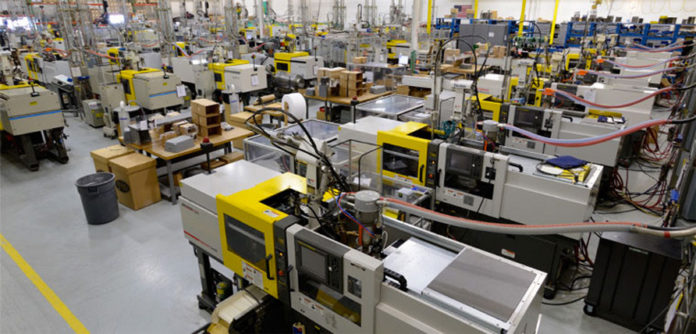
Injection molding has been one of the most used manufacturing processes in our civilization ever since the first machine created by John Wesley Hyatt and his brother. This was almost 150 years ago and we still use machines that work very similarly to the one John Wesley Hyatt created. Although, there have been many technological advancements that have made the whole process faster, more accurate, and efficient.
The first machine could only use plastic as an injection material and had very little capacity too. John Wesley thought of the idea of pushing the material through a heated cylinder directly into a mold. At first, the machine was pretty basic and could only create very simple products such as buttons and cups.
A couple of years later, Arthur Eichengrün, made the first injection molding press which would advance the industry even further. After Arthur’s innovation, came World War II and the need for this industry was higher than ever before. Parts for military trucks, tanks, airplanes were needed and the market sky-rocketed. Most of the technological advancements were made because of the constant push for higher-quality and reliable weapons.
If you are interested in learning more about the injection molding industry, here are some of its most important technological advancements.
Gas-assisted
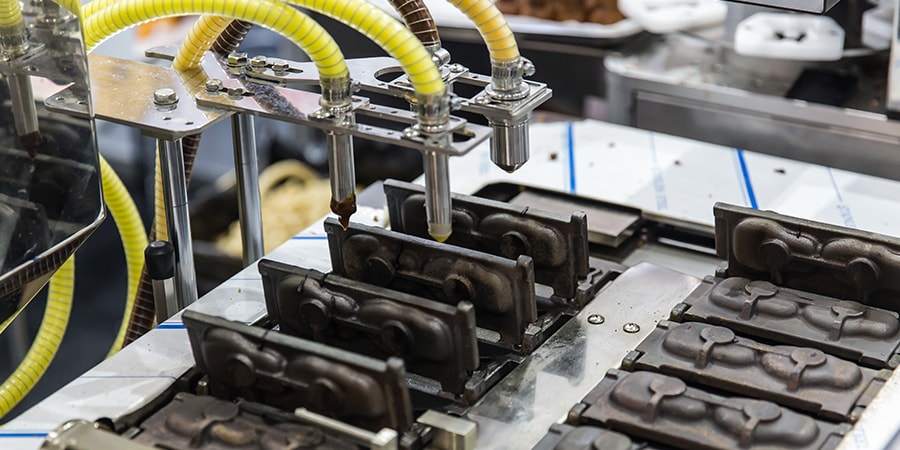
The first machine by John Wesley Hyatt used a plunger to push the plastic into the mold. Since then, we have made a lot of different ways to improve this process. The most common way to push the material into the mold today is through the assistance of gas. The most commonly used gas is nitrogen. The pressurized gas pushes the material fast enough to fill in every section of the mold which ensures that the final form of the product will be as planned.
Keep in mind, companies around the world have patented many different ways of using pressure for injection molding. In other words, there may have been a lot of technological advancements in this part of the industry, without us even knowing. These patented processes are what make today’s products so high-quality, durable, and reliable.
Foam injection
This might be one of the most important advancements in the industry because it helps the manufacturer achieve the highest possible structural resistance and integrity in their products. This process also removes the need for die-cutting entirely which means companies can save a lot of money by skipping certain steps for soft foam products.
Most foam products made from this process work much differently than say, sponges.
They have a much better ingress protection rating which means that water will have a hard time entering and mold won’t be able to build up. Bacteria will have a much harder time entering this type of foam.
With this method, the foam is created to be much more durable and stronger. Tearing this with your bare hands will be almost impossible. You would either need a very sharp cutting knife or pliers. If you are interested in all of the different processes of injection molding, you should check out qmolding.com
Thin-wall
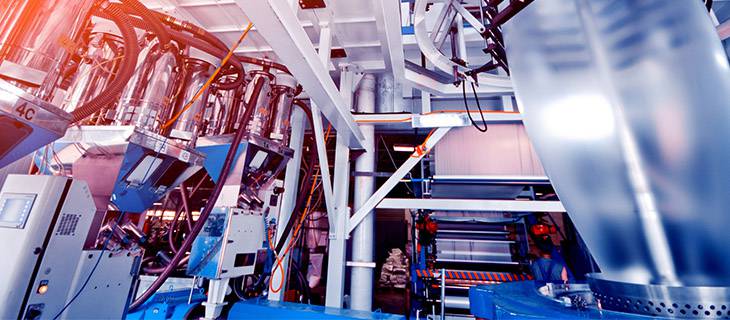
The thin-wall method was originally invented to help companies save on materials and to reduce the time needed to finish the process. This is usually used by bigger manufacturers that have to mass-produce plastic parts for many countries around the world. The products that come out of this method are very thin and light which makes them easier and cheaper to ship across the planet.
The cost of the thin-wall method is much lower than any other on this list and the machines are cheaper too. Because of the light work the machines have to endure, they are much less prone to problems or breaking.
However, while the plastic parts are thin and light, they are not as durable as they would be with gas-assisted injection molding. Their structural integrity is low and resistance to outside influence is much lower too.
RIM
Reaction injection molding is very similar to the original process expect the fact that a different resin is used called a thermosetting polymer. According to www.polychemistry.com Companies that use the RIM method are those that aim for more flexible, but strong products too. The advantage of these parts is that they can be easily applied with a coat of paint that will stick for a much longer time than usual.
The machine also has a much faster cycle time which is always an advantage.
Unlike thin-wall injection molding, with the RIM method, the plastic parts created are lightweight but have high structural integrity too. Their resistance to outside factors is much higher. The only downside to the RIM process is that the materials used in it are much more expensive. This is why many companies that are mass-producing plastic parts avoid it.
Die Casting
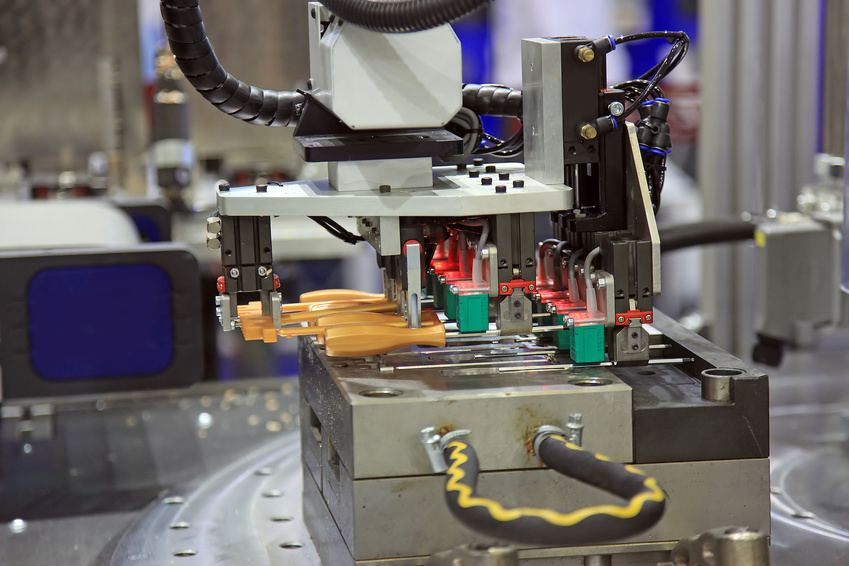
The difference between die casting and the original injection molding is the material that is used. To be more specific, instead of plastic, a metal such as zinc, aluminum, magnesium, copper, lead, and tin are used. These metals are heated up until they start melting. This molten metal is then forced by pressurized gas into a die. The mold is usually made out of steel because it is the cheapest material with the highest melting point.
Die casting is widely used in many industries because it provides very accurate and high-quality products. Most aero and car manufacturers practice die casting. The advantage of this method is that it is very dimensionally accurate. This cannot be said for all of the other methods of injection molding. The cast products that come out of die casting are also very smooth which is always a good thing. The production rate is also very high which helps companies save a lot of money.
However, there are some disadvantages too. For example, the machines and all the other equipment needed to practice die casting can be very expensive. Investing in die casting can be very risky which is why many people avoid it.
There are many other different methods of injection molding, but we believe that these are the most impressive technological advancements in the industry.