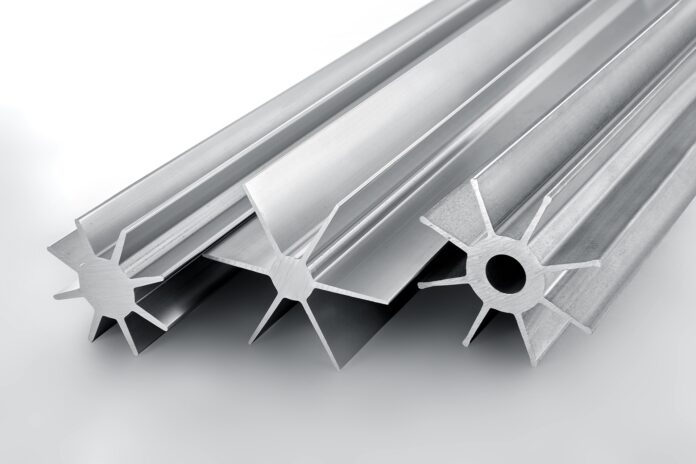
The extrusion is one of the most important processes in any industry as you need to choose the right material. When it comes to alloys, you need to be very particular about them, but one of the most recommended alloys is the aluminum alloy as it is a strong but light metal.
In the aluminum family, the member of the 7000 series is more popular, especially the 7075 aluminum. This alloy has got greater strength, and even when compared to the other steel, the material tends to be harder.
So, if you haven’t heard about this 7075 aluminum extrusion, then gain some knowledge about this metal, and find out why is it so popular in the industry.
Why 7075 aluminum is popular?
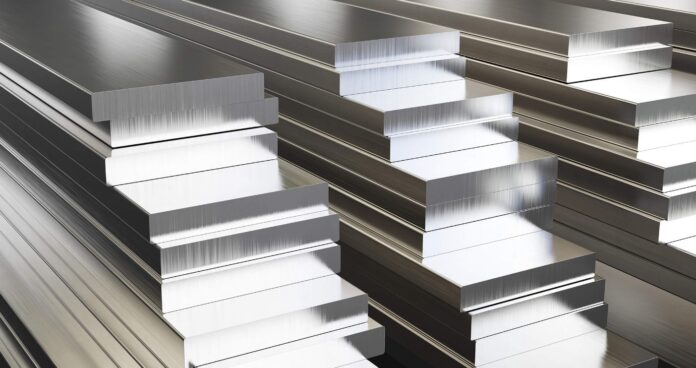
7075 aluminum is considered one of the strongest aluminum alloys, and even we can say that the alloy is stronger than much low-grade steel. The strength and durable properties of the material make them more popular in the industry.
So, when it comes to 7075 aluminum extrusion, it offers excellent mechanical properties, anode reaction, and also high corrosion resistance. Considering these properties, it is the most recommended material in the aircraft industry and other high-stress structural parts.
According to FONNOV, the 7075 aluminum extrusion is widely used in the mold processing, mechanical equipment, fixtures, and other such applications. It is an ideal option when it comes to challenging use, and are the most common alloys in industries like marine, automotive, aerospace, bike frames, ski poles, climbing equipment, and so on.
The 7075 aluminum extrusion is made of aluminum, zinc, and magnesium alloy. Let’s get to know about the composition of materials present in the 7075 aluminum extrusion (density > 2%),
- Si 0.40
- Fe 0.50
- Cu 1.2-2.0
- Mn 0.30
- Mg 2.1-2.9
- Cr 0.18-0.28
- Zn 5.1-6.1
- Ti 0.20
- Others 0.15
Finally, the remaining percentage will be Al.
The major element in the 7075 aluminum is zinc, as zinc is added to increase strength. All these chemical compositions of aluminum will make 7075 aluminum with good ductility, high toughness, and good resistance to fatigue.
Comparison of 7075 with other alloys
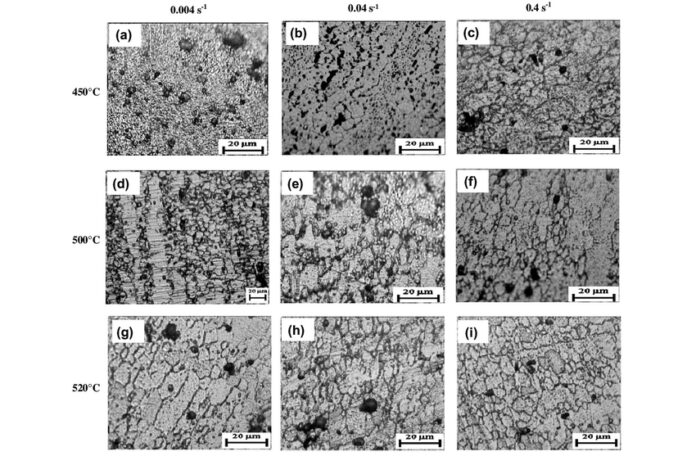
The major advantage of the 7075 aluminum extrusion is it offers higher strength, and also it comes with particular applications.
- As the 7075 aluminum comes with greater mechanical strength, so it is mainly used in the aircraft industry. Even the 2000 series alloys can be used in the aerospace industry, but others won’t offer high stress/strain resistance like 7075 aluminum alloy
- The 7075 alloy is a lighter material than steel, so it becomes another advantage of having 7075 aluminum alloy in the industry
- The alloys in the 6000 series will deform easily, but the 7075 aluminum alloy is able to withstand high pressure and undergoes more impact without any deformation
- The 7075 alloys offer high yield strength than the 6061 aluminum alloy, and this is due to the chemical composition and heat treatment
6 Things to Consider for 7075 Aluminum Extrusion
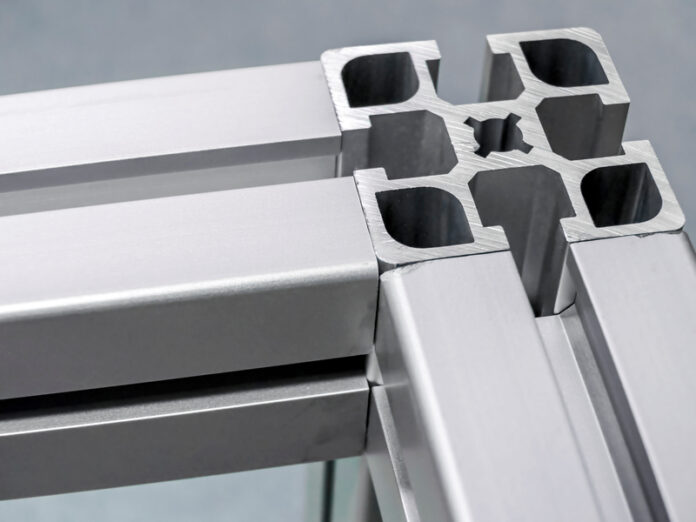
The extrusion is one of the important and serious processes whatever the alloy you used for. When you choose the extrusion process, you can make aluminum extrusion of different sizes, and even you can change a lot of variables to consider. Here are the basic things you should consider for the 7075 aluminum extrusion.
Type of alloy
As the 7075 aluminum comes with greater strength, so it is one of the most commonly used materials in the extrusion process. When compared to the other alloys, it offers the highest mechanical strength, and is most recommended for designing extrusion pieces.
Temper
While creating the extrusion of aluminum alloys, the temper of the alloys is mostly used. The 7075 is a little difficult for the extrusion process, so you have do it carefully or else it will result in a poor surface finish.
Thickness
While doing the extrusion process, the thickness of the wall of the extrusion is more important so you need to consider consistency and uniformity. The 7075 aluminum alloys flow through the extruder at an even rate, so it offers a uniform thickness shape.
Tolerances
The main rule to follow while doing the extrusion process is, that the larger the dimension of the shape that you want to create, the wider range of tolerance is required.
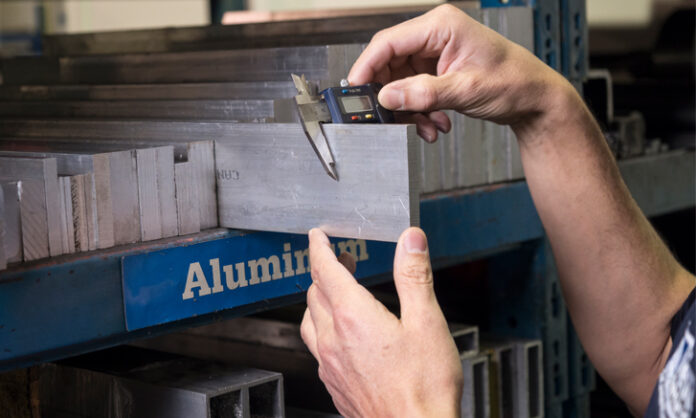
Corner Radii
If you want to create a successful aluminum extrusion, then it is important that you should know the corner radii. In most cases, the aluminum manufactures round or unsharp corners, so you won’t get the extrusion that is lesser than the radii 0.005” which is the rule of the thumb.
Finishing
Once you are done creating the aluminum extrusion pieces, then the added touch is the most important one that you should do. Depending on the extrusion you make, the finishing process will differ as there are huge methods of the finishing process.
The finishing applications include anodizing, chemical conversion coating, cutting to length, machining, punching holes, drilling holes, center-less grinding, and other finishing applications.
Benefits
- Even though the 7075 aluminum is the hardest material, still it can be extruded
- Offers good plasticity after the solution treatment
- Offers excellent heat treatment strengthening effect
- Shows high strength below 1500C
- Particularly useful for low-temperature strength, poor weldability, double aging, and stress corrosion cracking tendency will improve the anti-SCC performance
- Even though the 7075 aluminum shows lower resistance to corrosion when compared with other aluminum alloys, but still offers corrosion resistance to the 2000 series
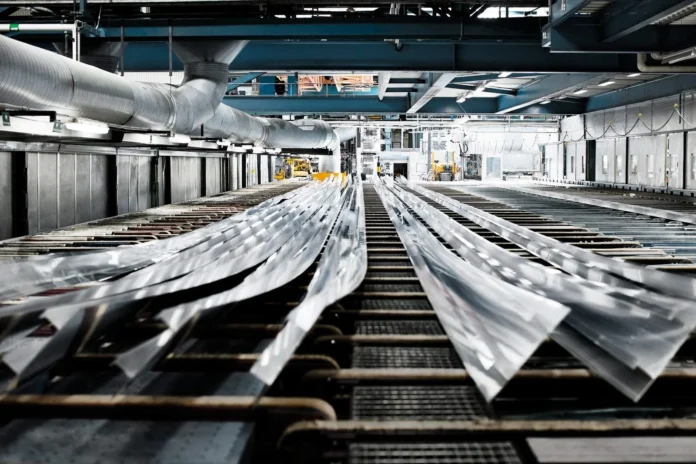
Final thoughts
The 7075 aluminum extrusion is known for having a higher strength, so this type of alloy is the most commonly used alloy in the aerospace industry. This will be an excellent material for your industry if you are looking for an alloy that has a high strength-to-density ratio.
The 7075 aluminum alloy costs are high, and also the process of extrusion is a little harder when compared with other alloys, still, this is one of the most recommended aluminum alloys. For extruded aluminum and more, view here for the selection of shapes and sizes.