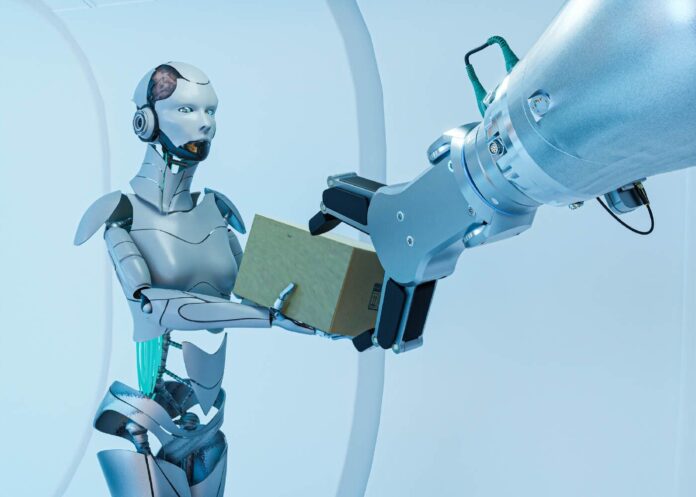
In the ever-evolving landscape of robotics, two distinct categories have emerged: cobots, or collaborative robots, and traditional robots. The rise of automation has revolutionized industries, offering efficiency and precision like never before.
However, amidst this transformation, the concept of collaboration has become increasingly significant.
In this article, we delve into the realm of cobots and traditional robots, exploring their characteristics, applications, and, most importantly, the advantages of collaboration in robotics.
Understanding Cobots and Traditional Robots
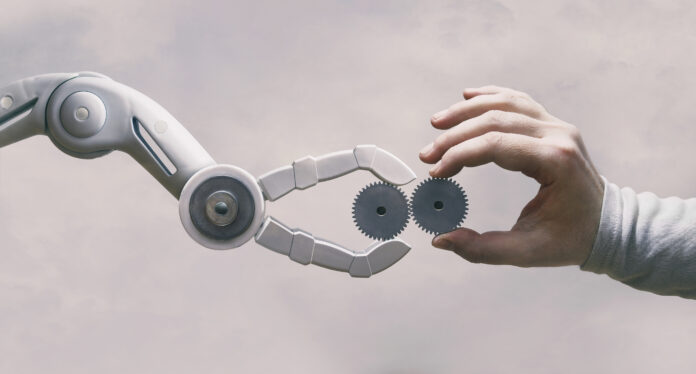
Cobots (Collaborative Robots)
Collaborative robots, or cobots, represent a new generation of factory robots designed to work alongside humans in a cooperative manner. Unlike their traditional counterparts, cobots are equipped with advanced sensors and safety features that allow for safe interaction with human workers. These robots are characterized by their ability to perform tasks in close proximity to humans without the need for safety cages or barriers.
Cobots find applications across various industries, including manufacturing, healthcare, and logistics. Cobots in manufacturing assist with assembly, packaging, and material handling tasks, enhancing productivity and efficiency on the factory floor.
In healthcare, they aid in patient care, such as assisting surgeons during procedures or delivering medication to patients. Additionally, cobots play a crucial role in logistics, streamlining warehouse operations by automating tasks such as picking, packing, and sorting.
Traditional Robots
Traditional robots, on the other hand, have been a staple in industrial automation for decades. These robots are typically large, stationary machines programmed to perform specific tasks with high speed and precision. Unlike cobots, traditional robots often operate in segregated areas, away from human workers, due to safety concerns.
Traditional robots are commonly utilized in manufacturing for tasks such as welding, painting, and machining. Their high-speed capabilities make them ideal for repetitive and labor-intensive processes, allowing manufacturers to increase production efficiency and quality.
Advantages of Collaboration in Robotics
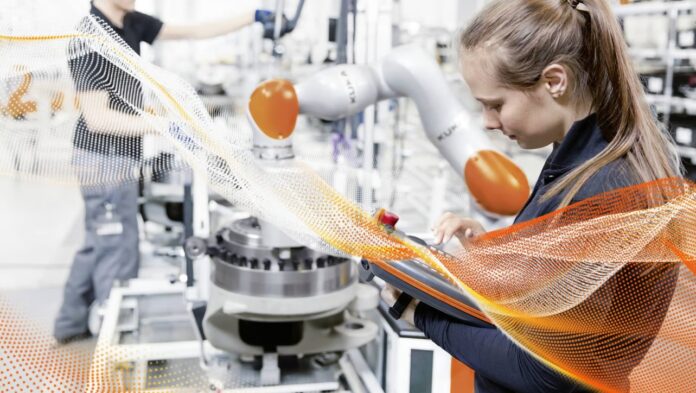
Safety
One of the most significant advantages of collaboration in robotics is improved safety in the workplace. Cobots are equipped with advanced sensors and safety features that allow them to detect and react to the presence of humans in their vicinity.
This enables cobots to work safely alongside human workers, reducing the risk of accidents and injuries on the factory floor.
In contrast, traditional robots operate within confined spaces and often require safety cages or barriers to prevent accidents. These physical barriers can restrict access to the robot and impede workflow, leading to inefficiencies in the production process.
Flexibility and Adaptability
Another advantage of collaboration in robotics is the flexibility and adaptability offered by cobots. Collaborative robots are designed to be easily reprogrammed and reconfigured to perform different tasks, making them highly versatile in dynamic manufacturing environments.
Cobots can quickly adapt to changes in production requirements, allowing manufacturers to respond swiftly to fluctuations in demand or product specifications. This flexibility enables businesses to optimize their production processes and improve overall efficiency.
In contrast, traditional robots are often dedicated to specific tasks and require significant reprogramming and retooling to adapt to new requirements. This process can be time-consuming and costly, leading to delays in production and increased downtime.
Performance and Efficiency
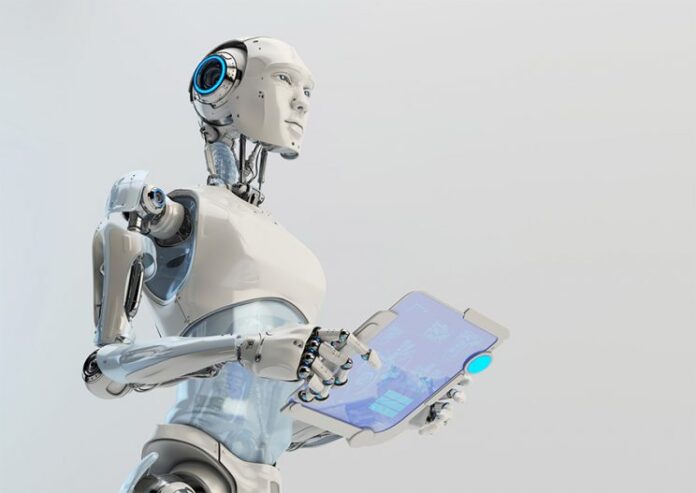
Speed and Precision
When it comes to performance and efficiency, both cobots and traditional robots excel in their respective domains. Conventional robots are known for their high-speed capabilities and precision, making them ideal for tasks that require repetitive and accurate movements.
However, collaborative robots offer a unique combination of speed and precision, coupled with the ability to work alongside human workers. This collaborative approach allows cobots to perform tasks with a level of dexterity and flexibility that traditional robots may lack.
In industries such as electronics manufacturing, where precision is paramount, cobots are increasingly being deployed to assist with delicate assembly tasks. These robots can manipulate small components with precision and accuracy, resulting in higher product quality and fewer defects.
Task Automation and Optimization
Collaboration in robotics also leads to improved task automation and optimization. By working alongside human workers, cobots can automate repetitive and labor-intensive tasks, freeing up human workers to focus on more complex and value-added activities.
In manufacturing, cobots are often used to handle tedious tasks such as material handling, assembly, and inspection.
By automating these tasks, businesses can increase their production throughput and reduce the risk of errors, leading to improved overall efficiency.
Human-Robot Interaction and Workforce Integration
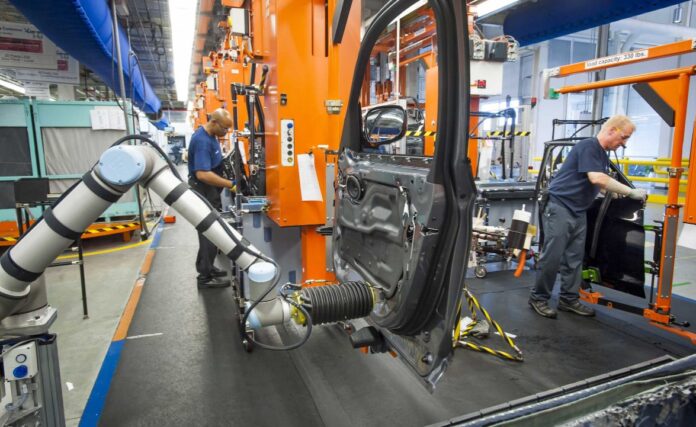
Collaborative robots play a crucial role in improving ergonomics and the work environment for human workers. By automating repetitive and physically demanding tasks, cobots help reduce the risk of musculoskeletal injuries and fatigue among workers.
Furthermore, the collaborative nature of cobots enables them to work alongside human workers in close proximity, creating a safer and more collaborative work environment.
Unlike traditional robots, which are often confined to separate workspaces, cobots can seamlessly integrate into existing production lines, enhancing workflow and efficiency.
Another advantage of collaboration in robotics is the opportunity for human skill enhancement and training. Collaborative robots can assist human workers with tasks that require specialized skills or training, allowing workers to acquire new skills and improve their capabilities.
In manufacturing, cobots are increasingly being used to train new employees and upskill existing workers. By working alongside cobots, human workers can learn new techniques and best practices, ultimately improving their productivity and effectiveness on the job.
Conclusion
In conclusion, the advantages of collaboration in robotics are clear. Cobots offer a unique combination of safety, flexibility, and efficiency that traditional robots may lack. By working alongside human workers, cobots enhance productivity, improve safety, and create new opportunities for innovation and growth.
As we look to the future, collaboration will continue to be a driving force in the field of robotics, shaping industries and society in profound ways.